(The Business Landscape of future has tremendous opportunity for those who are willing to lay strong foundation based on fundamentals facilitated by Technology & Digital Assets)
Authors work has off late been supported by Davos Agenda 2021 as reported by World Economic Forum in its recent article Manufacturing Reimagined: from improved productivity to profitable growth published on 18th Jan’21, compiled by Katy George, Sr Partner, McKinsey & Co.
In a recent poll created by one of the Managing Director of a Tech Companies to know the reason why India has low adoption of the technology, the result is as under-
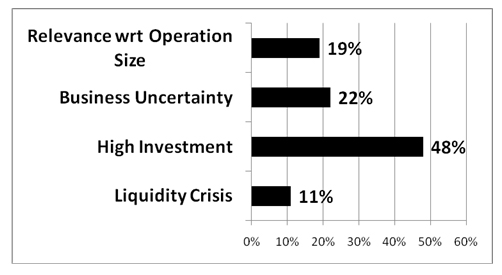
The result perfectly reads when combined with PwC survey report of Dec’19 which said more than 90% of Indian CXOs have no idea about the requirement of Industry 4.0 and risk associated with it. The divided opinion proves Industries are guided by wrong notion. Various reasons cited by participant industries admittedly and evidently have tried to find an excuse.
First and foremost, it has nothing to do with size of operation. Just like mobile phone does not discriminate between rich & poor and is essential for all, digital assets are mandatory for all.
Business Uncertainty is not limited to pandemic. In VUCA world with growing business complexities, intense competition and ever changing macro economy, business is at war today. Uncertainties are set to grow through passing days. Without finding an excuse, aligning the business with global norms will help to stay relevant.
Cyber Physical Assets are investment intensive to those who have no idea about requirement of Industry 4.0.
Liquidity crisis has been a passing phase out of lockdown and economic activity closure that has impacted all, be it job holder or business men. Surprised with the fact, Indian industries have not been able to sustain one/two months of lockdown and sought stimulus from the govt. I wonder how they sustain Lockout for months together! Nevertheless, it is now eight months that economic activity is revived and manufacturing activity has touched PMI score of 55, highest in last one year.
Unless industries cross the bridge of their insecurities, they can’t begin to explore possibilities to touch the glory of the sky.
Dannis Nelly, Chairman, Price Waterhouse Cooper in 2018 has said- “If India can create capabilities for growth and new solutions, the opportunities are limitless”.
Technology is investment intensive to those who have no clarity about the requirement of Industry 4.0.
Assessing the requirement
Working in right spirit to develop their own industry will enable Business Leaders stay relevant and grow in VUCA conditions.
To the benefit of readers, it is appropriate to mention here that Industry 4.0 has two aspects- Technological and Functional. Mere adopting tools of AI are not sufficient to yield desired results unless supported by robust performance pillar. Machine can only provide insights to work upon, not the judgement or ingenuity. People will.
The purpose of Industry 4.0 is to improve productivity. Higher productivity is not subject to higher production numbers, less/no machine stoppages due to any reason or less labor cost. Production numbers is always limited to installed machine capacity. Reducing labor cost is also a myth. Reduction in labor head count does not mean reduction in labor cost. Remote controlling of machine and production requires separate set of qualified white collar supervisors who are set to replace blue collar workers that will either increase or keep the employment cost at par. Provided further, cost reduction measures have its limitation, upto optimum level. What next? As the say goes, being rich is easy, but is equally difficult to stay rich.
Productivity is subject to economic parameters and factors of production that governs the profitability of the company. Common scale growth is essential for return to scale. This is one area that is being grossly ignored across industries- be it large, medium or small. Misalignment of factors and cost parameters is resulting into higher cost of production to make industries cost-inefficient and uncompetitive has been noticed across our studies. Varied performance & Operational gains have been found to be fortuitous. Tools of AI are meant to integrate process for operational efficiency and to bring performance stability determining determinant costs on real-time basis. Reading operational economic fine print is mandatory for being cost efficient and competitive. Manufacturing is not limited to assembly of parts or preparing input basket for value added product. Profit and Growth is not limited to scaling sales revenue, as is being commonly perceived, ignoring operational parameters.
Provided further, there is no one-size-fit-all solution for all industries. Every manufacturing entity is governed by its own dynamics based on product and process. Outsourcing adoption of tools of AI to tech companies with standard product/services is certainly a waste of money. Admittedly and evidently, they are charging a mid size unit to the extent to Rs 5 Crore. Installing sensors in the machine and loading algorithm is beyond the scope of Tech companies and will fetch further cost. All the tools of AI, or Cyber Physical Assets will not be required by every industries. The requirement need to be assessed by the organization based on its own requirement and dynamics.
The onus therefore lies on organizations to assess the requirement of tools and capabilities of talents employed with it rolling out HR 4.0 initiative.
There cannot be any other best person other than Business Leaders themselves who are aware of business dynamics, process flow etc to assess the requirement of tools of AI to integrate with the process.
The Winning Leap
“To support any hope of lasting competitive advantage, companies know their operations must achieve more than ever before….. The Fourth Industrial Revolution is no longer hype: it’s fully here, enabling real gains in productivity, sustainability, agility and speed-to-market. Manufacturers that choose to reimagine their growth strategies by embracing the advances are setting new benchmarks. Those that do not risk falling behind in an uncertain and increasingly threatening competitive landscape.”– World Economic Forum on Davos Agenda 2021
Best of Technology or Cyber Physical Assets at several hundred millions cannot be the only winning leap. Fundamentals of Business and Operation are not subject to any technology. Contrary is true.
So far as technological benefits are concerned, Designing and Prototyping products based on customers requirement & additive manufacturing, predictive maintenance is the definite help.
So far as functionalities are concerned, market or customer will continue to respond based on your cost & price, unless you have some unique product on offer as competitive advantage.
Adding technology without being aware of how to utilize the best out of it will be futile and complete waste. Huge data generated need to analyzed. Source of reliable data must be known to integrate. On what operational economic parameters you or your team should analyze the data must be learned.
According to my research 99% organizations are not aware of Relative Cost-Price threshold to determine the cost and price despite having ERP system in place. Business Plans are broadly assumptive, even across many MNCs.
Redefining and Re-imagining Cost Structure is the definite winning leap. In days to come, many or most companies will have most of the available technology and will be a common feature. So the cost parameters are bound to be governing factor for having competitive advantage through perfect utilisation of technology.
The purpose of technology is therefore more about Business Analysis, Business Intelligence and Decision Intelligence than Technological advancement. Improving productivity across all the resources is the requirement of the day. Analysis needs to scale across all parts of the business from HR, sales, Finance, Materials, Marketing to the Manufacturing floor.
As per European Productivity Council Productivity is a mindset. Low Cost Manufacturing therefore is more of a mindset than technological intervention.
Industry 4.0 does not require PhD or huge investment. What it requires a little bit of courage to get the hands dirty to begin with. Developing capabilities, performance pillar & required skill, inter-alia, Modelling Scientists and Decision Scientists, is the first step towards new normal. Once value stream mapping is done and technological requirement is assessed based on business dynamics, you can build the infrastructure in-house at much lower cost. Doing so, you can save-
• 90% towards Capex
• 20-30% towards Opex, inter-alia, operational cost on recurring basis y-o-y
• Software maintenance & up gradation cost to the extent of around 10% of developing algorithms each year.
You need to follow AI Investment rule
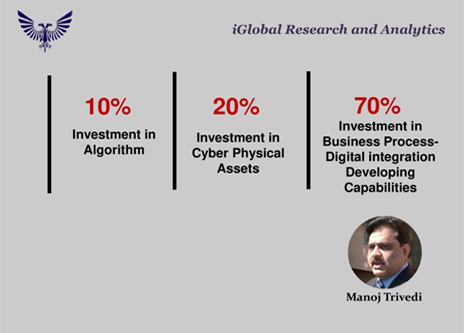
You must learn how Industry 4.0 works, asses requirements and develop relevant capabilities/skill/performance pillar to control Capex Cost and for best utilization with competitive advantage. Your ROI will be subject to optimization of operational cost and higher returns across resources.
While everyone is engaged in promoting technology, no one considers functional aspects or performance pillar, the essence & fundamental is without which technology shall be lame.
Secret of change for success is to focus all your energies not on fighting the old, but on building the new. Practicing new has to be a matter of habit that needs to be inculcated & imbibed over a period of time before opting for the technology and assessing the requirement of tools of AI.
Attending ordinary programs – Webinars/Semiinars/Workshops/Trainings cannot pay off unless every individual employee of any organization is demonstrated and handheld for focussed guidance developing capabilities integrating with process suitable for growth utilising digital means. Onboarding suitable expert will certainly help matters to care & develop your organization like a child.
Incidentally, as per Subsection 6 of Section 149 (a) of Companies Act 2013, Independent Directors are supposed to be an expert and guide to add value to stakeholders.
About the Author

With four decade bottom up industrial leadership Manoj Trivedi, Founder Director & Business Mentor at iGlobal Research & Analytics, is the only facilitator engaged in developing capabilities, performance pillar and required skill of Industry 4.0 for being cost efficient and competitive while helping industries through value stream mapping & assess requirement of tools of AI based on its dynamics. He undertakes short/long term contract as may be required in preparing industries for the challenge. He may be contacted at (91) 9051831961. Alternatively, you can reach him at [email protected].
Also read my earlier articles
