One Factory One Solution
Have you ever tried listing the solutions and techniques available today to manage a factory? It is truly maddening. You may wonder why a factory cannot have just one inexpensive and complete solution to manage all its affairs.
The reason is simple, one critical function of deciding which activity of which job to do now and on which machine is still done manually. This “scheduling decision” making, to figure out the next activity to do on a particular machine, must be repeated whenever any currently running activity is reported as over.
A factory is a connected unitary structure. All factory functions influence and are in turn influenced by the scheduling decisions made. Somehow we missed automating this central and critical scheduling decision making core. Automating peripheral factory functions serve no purpose as they cannot function properly sans the central scheduling decision making core. However, once the central scheduling decision making core is automated, all peripheral functions are naturally automated.
Currently prevailing management techniques (including industrial engineering as a subject) too are of no help as they are all based on a hidden assumption that factories will “mass produce” things. Mass production means following a standard work flow and repeatedly doing the same set of activities over and over again, as represented by the assembly line. The emphasis, thus, is on streamlining flow and increasing execution efficiency of individual processes.
Unfortunately, factories today seldom mass produce. Order quantities have dramatically shrunk and product variation has gone up. Orders seldom follow a standard work flow and each order requires a different set of short duration activities to be executed. So any gain on account of streamlined flow and efficiently doing individual activities is lost due to the scheduling chaos that ensues. Scheduling complexity increases exponentially as the number of activities go up making even managing a modest shop floor humanly impossible. The answer again is in automating the central scheduling decision making core.
The purpose of this article is to briefly acquaint you with a solution built with an autonomous scheduling program (ASP) that truly automates the central scheduling decision making core of a factory. Serendipitously, when the central scheduling decision making core is automated, the ability to predict the future, that is in sync with the present, too becomes possible.
Having such a solution opens up a whole new world of possibilities hereunto considered impossible. This solution fulfills the dream of a lights-out future factory that we today can only imagine but can never realize. The ASP becomes a true digital twin of the entire factory. The ASP micro manages the real factory while simultaneously predicting the future schedule in real time. It controls, aligns and adapts itself to the real factory in real time.
Factory manager’s day-to-day involvement in job execution is optional rather not needed once execution guidelines for the ASP to follow properly set. Factory manager can now focus on planning ahead instead of just reacting to what happens. Planning ahead further enhances the reliability of the predictions made by the ASP. The whole factory works like a well-oiled machine with clock-work precision to convert raw material into customer ordered final products.
Do you find it difficult to believe that such a solution really exist? No problem, just contact the author to request for an evaluation version of the solution that you can install on your PC to check out. The evaluation version comes bundled with documentation to enable you to self-configure the solution to fit your factory.
The solution works in any factory, whatever it produces and whatever be its size. If water represent your orders and the factory machines and resources the terrain, the solution finds the most optimum path for the water to flow. In other words, to complete all orders as fast as possible (ASAP). Change factory specifications, and the solutions finds a new optimum way of completing all orders ASAP. Please try it.
What it takes to create an ASP?
Automatic scheduling is only possible if we know unambiguously “what-to-do” for each order. Call it the work flow steps required to ultimately realize the final product the customer has ordered for. This “what-to-do” must have all information about each activity, like the input and the output an activity needs or creates; the duration, the wastage incurred, the cost of doing each activity, the supporting tools and fixtures needed and just about everything.

Unfortunately, current methods to depict workflow, namely, the activity precedence diagram and the bill-of-material are both wrong and incomplete. Activity precedence diagram connects the predecessor activity to the successor activity but is silent on what the successor activity needs from the predecessor activity (Figure-1).
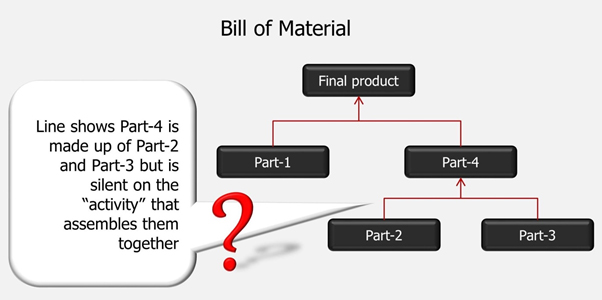
The bill-of-material talks of sub-parts that make the whole part but is silent on what activity assembles or transforms these sub-parts into the whole part (Figure-2).
We invented a new workflow representation called the CT diagram (see figure–3). If procurement is deemed to be the first activity then raw material the job need is the output it creates. Thereafter, subsequent activities will add value to the raw material, and work-in-progress created en route, until the final product the customer has ordered for is created.
Only knowing about activities is not enough. ASP must also know “where-to-do” the activities. Meaning a complete job definition should include “where-to-do” information as well. CT diagram clubs the “what-to-do” and “where-to-do” information making it a complete job definition, specific to a given job to be executed in a given factory.
Just having access to all job definitions also is not enough, ASP must have access to factory information not specific to any job, like holiday timetable, off-shift periods and anything that affects the schedule. Non-job specific factory information is mostly static requiring occasional updating.
Armed with all job definitions under execution and the non-job specific factory information, the ASP can easily schedule production of even the most complex factory with clock-work-precision 24×7.

Creating an ASP and figuring out how job and factory information could be represented is complex but doable. Once developed using the ASP and configuring it to suit any factory is very simple.
Working of the ASP
At any point in time a factory has several jobs (customer ordered as well as maintenance and repair jobs) under execution. Meaning ASP already has a set of job definitions uploaded with it. It also has access to non-job specific factory information enabling it to manage shop floor scheduling 24×7 (see figure-4).
Operators are given access to an application running on some hand held device or a computer kiosk positioned on the shop floor. This is the “work center console” interface (WCC). Shop floor will have several WCC located strategically to cover all machines. All WCC are in real time communication with the ASP enabling operators to notify activity completion and know what the next allotted activity is. WCC also provides features to tackle abnormal situations like breakdowns and stoppages. WCC shows a timetable of future activities lined up and details of activities already completed on each workstation assigned to it.
The “job study wizard” application (JSW) is used to define new jobs. Most factories deal with repeat orders or orders having a common workflow. Meaning, it is possible to create a library of all possible job types encountered. Defining a new job could be as simple as opening an already defined similar job, making minor modifications to it, and saving it as a new job. Maintenance and repair work too are activates as they keep a given machine busy. So they too are defined as jobs in the JSW.
JSW validates each job definition to highlight errors for user to correct. JSW can be used to upload valid jobs to the ASP for execution. JSW comes equipped with a simulation facility. Instead of uploading a new job for execution, we request the latest factory status from the ASP, and use it locally to run a simulation.
Factory manager can tap into the ASP using the “shop floor display” interface (SFD). This is a real time single window access to the real factory from anywhere. The SFD has several views to enable the factory manager to see what is happening now and in the future. SFD can also be used to control job execution.

Some screen shots of the actual solution
We can define a CT diagram job using the Job Study Wizard (JSW). JSW is the salespersons’ application. Each Salesperson has one. Figure-5 shows a CT diagram defined to make classroom bench in a carpentry shop. Pink rectangles represent tasks whereas blue squares the components they create as output or accept as input. The maroon square is the final product component. Green rectangles represent sub-workflows to make the bench frame or the boards functioning as the seat or back of the bench. One can view details of the sub-workflow as well as seen in figure-6.
JSW can be user-configured to define jobs specific to any factory. Estimation of cost, duration, wastage, raw material required and every imaginable job characteristic is possible. The CT diagram is the workflow, the estimation tool and the actual execution plan that the ASP uses to get the job executed in the factory. Once the job is over CT diagram job becomes a repository of all information about how the job was executed.


Jobs defined as a CT diagram are saved to a file. These files can be shared with other JSW users and ‘saved as’ to define several new jobs. Whenever a job matures for execution, its saved CT diagram job file can be scheduled for execution from the JSW itself. The ASP then ensures the job gets executed in the factory.
Individual tasks of the job are electronically sent to the concerned machine via its assigned WCC. WCC is the operator’s application. Several WCCs are strategically placed on the shop floor to cover all workstations. Operators notify task progress and completion. ASP communicates with each workstation of the factory in real time. Operators’ have full information about the task to undertake: the inputs needed, the outputs to be created, and all other data needed to execute the task. Figure-7 shows a WCC screen shot detailing all information for a particular allotted task.
When operator notifies current task completion from the WCC it in turn triggers allotment of a new task. This cycle of task allotment its completion notification and next task allotment continues as long as the factory works.

Factory managers can monitor and control all scheduled jobs using the SFD. Factory manager sees a real time view of the entire factory with a detailed schedule prediction for all jobs under execution.

Figure-8 shows the Gantt chart view. The Gantt chart is auto refreshed on each reschedule happening every minute. There is no need and no facility provided to manually change or correct the Gantt chart as rescheduling is truly automatic. The scheduled created is guaranteed to be the best and always feasible. That makes SFD a true digital twin of the shop floor as what the Gantt chart (and other real time views as well) show is what is really happening on the shop floor.
SFD has many other views. One of them is the “factory schematic” view. It enables factory manager to drill down to a particular workstation in the factory to see what tasks are running on it now, what tasks were done in the past and those lined up for future execution.

One starts with the world map view showing all plants of the factory and drills down to a particular workstation of choice. Figure-9 shows the Carpentry shop seen as a little red square on the world map.
Double clicking on the plant square enables one to see the carpentry shop layout as seen next in figure-10
Double clicking on a particular department shows the machines and workstations within as seen in figure-11.
Double clicking on a particular machine one sees a complete list of tasks. Those done in the past, those currently running now and those lined up for future execution with idle times in between also highlighted. See screen shot in figure-12.
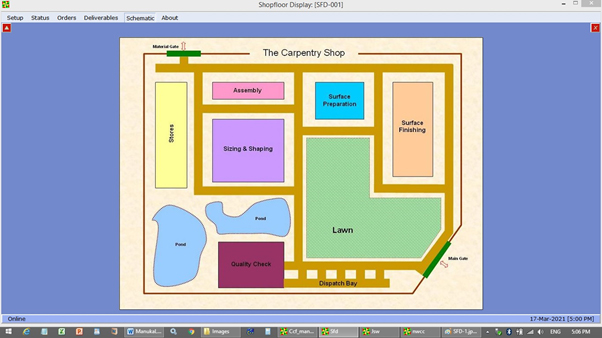
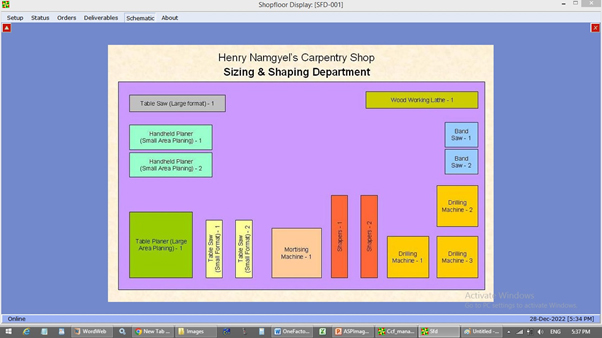
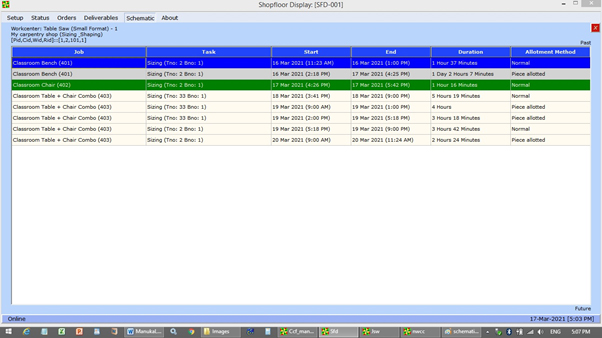
Yet another view called “deliverables” enables one to monitor jobs by delivery date-time commitments. One sees a list of jobs colour coded according to on-time or delayed status. See figure-13.
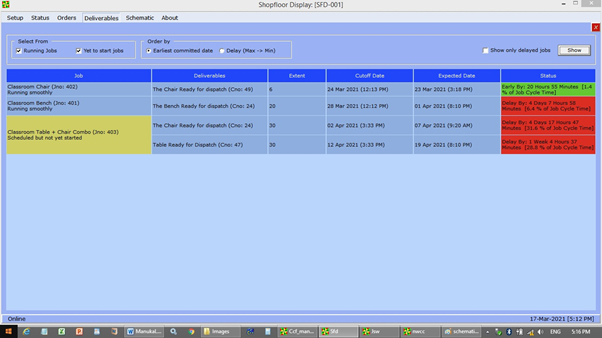
Green jobs are in-time whereas red ones are delayed. The same SFD can be used to bring about changes in order to expedite delayed jobs.
Yet another view “job-at-a-glance” enables one to see complete details of a particular job from start to finish (figure-14). Individual tasks of the job are shown as proportionately long lines stacked vertically over the time line. Yellow lines represent committed date-time. You see two yellow lines in the image below as this job has two deliverables, viz., the Table and the Chairs, each having its own committed due date represented by the yellow line. Seeing yellow lines confirms the job is already delayed. Investigative analysis displays top five tasks of the job ordered by duration and waiting time.

This one inexpensive solution obviates the need of having any other factory management system as it offers full end-to-end functionality from job estimation until final dispatch. The product provides a standard framework that the user can configure to suit any factory. Only fundamental logical and mathematical rules are hard-coded, everything else is user configurable. That makes for universal applicability of the solution to any manufacturing setup of any size.
This solution is unique as it is based on a novel concept of a CT diagram developed by the author. The key to autonomous scheduling is in fact this CT diagram representation.
About the author:
Mr. Laxman Chandrakant Marathe
Founder,
ManukaLive Research Center (MLRC)
Laxman is an electronics engineer with a post-graduation in industrial management from reputed institutes in India. He graduated from the Indian Institute of Science, Bengaluru and completed his post-graduation from the Indian Institute of Technology, Madras.
He started his career as an Industrial Engineer with Tata Steel at Jamshedpur. After working for almost a decade at Tata Steel he moved over as a Unit head of a commercial printer called Thomson Press (India) Limited at Faridabad, some 35 km south of New Delhi, India.
His almost two decade association with Thomson Press was a pure learning experience. He learned everything about the print and publishing business as well as got a firsthand feel of the real issues faced by a typical factory manager. It was during his tenure as a factory Manager that the idea of creating a scheduling solution based on the concept of a CT diagram took birth.
Over time the idea blossomed into a full-fledged solution concept. It was difficult anymore to postpone the urge to bring this solution into reality. So once his financial situation was fairly stable (April 2016) he decided to pursue his dream project.
He established the Manuka Live Research Center at his home town in Sangli. It takes a while and a lot of hard work to develop anything new. Sheer dedication and true passion were the only driving forces that kept the research center alive. All the effort and toil was well rewarded on seeing a real working solution take shape.
The next thing now is to make the solution available to those who need it the most: the quintessential factory Manager. As a factory manager myself once, I know how thankless and difficult this job is. With this solution in place factory managers can now breathe a sigh of relief. They can now concentrate on really managing the factory rather than just firefighting every day.
Mr. Laxman C. Marathe can be contacted at:
Email : [email protected]
Mobile : +91-9011098634
LinkedIn : https://www.linkedin.com/in/la
Twitter : https://twitter.com/lcmarathe