ERP and MES Integration Drives Digital Transformation for Semiconductor Manufacturers
Introduction
The manufacture of each semiconductor chip requires hundreds of processes. After sorting, the entire manufacturing process is divided into eight steps: Wafer Processing, Oxidation, Photography, Etching, Film Deposition, Interconnection, Test, and Package.
Chip manufacturing industries generally use MES to achieve daily process on system by tracking and gathering real-time data about the processes. It helps to manage production scheduling and sequencing, create an audit trail for track and trace, and deliver work instructions to shop floor workers.
Semiconductors are crucial components in a wide range of products, including computers, smartphones, televisions, cars, medical equipment, and many more. As technology advances, the demand for more powerful and efficient chips continues to grow, making the semiconductor industry one of the fastest growing and most important sectors in the global economy.
The semiconductor industry is characterized by rapid technological innovation, intense competition, and a high level of investment in research and development. So here to value add in semiconductor industries this article will give brief about how beneficial to integrate MES with ERP and what are the advantages of it.
Chip Manufacturing Process in Semiconductor Industries
Semiconductor devices are built up in a series of nanofabrication processes performed on the surface of substrates made from highly pure single crystal silicon. These substrates are usually known as wafers. Commonly used wafers include the 300 mm type, which offers the advanced miniaturization required for cutting-edge devices, and 200 mm type, which is better suited to the mixed, small lot production needed for devices for the Internet of Things (IoT).
The wafer surface is coated with resist (photosensitive chemical). Then the wafer is spun, causing a uniform layer of resist to be formed on the wafer surface by centrifugal force.
The wafer is exposed using short wavelength deep ultraviolet radiation projected through a mask on which the circuit pattern has been formed. Only the areas of the resist layer that are exposed to the light undergo a structural change, thereby transferring the pattern to the wafer. There are a variety of exposure units, including steppers, which expose several chips at a time, and scanners, which expose the wafer using a slit through which light is projected onto the wafer.
Developer is sprayed onto the wafer, dissolving the areas exposed to the light and revealing the thin film on the wafer surface. The remaining resist areas that are not exposed at this point become the mask for the next etching process.
In wet etching, the exposed thin film on the surface layer is dissolved using chemicals, such as hydrofluoric acid or phosphoric acid, and removed. This forms the pattern. There is also a dry etching method in which the wafer surface is bombarded with ionized atoms to remove the film layer. Resist can be stripped off at a wet station, which uses chemicals that remove the resist, or by aching, which removes the resist by inducing a chemical reaction using gases. The wafer is cleaned after the aching.
The wafer is separated into individual chips (dicing), the chips are connected to a metal frame called a lead frame using metal wire (wire bonding) and then enclosed in epoxy resin material(packaging).
Then Packaging is done, Chip packaging is the process of putting the integrated circuit die (Die) on a substrate that plays a role of load, leads the pins out, and fixes the package as a whole. It can protect the chip, enhance its electric heating performance, and help channel heat, improve performance, reduce power, and safeguard signal integrity. Then last Is shipping the product.
Limitation of using standalone MES in Semiconductor Industry
Data Management: The semiconductor industry generates a large amount of data, including product specifications, manufacturing instructions, test results, and process parameters. Without an ERP system, managing this data can be challenging, leading to data inaccuracies, data silos, and increased risk of errors and quality issues.
Poor Supply Chain Management: The semiconductor industry relies on a complex network of suppliers, contract manufacturers, and logistics providers to deliver raw materials and finished products. Without an ERP system, managing the supply chain can be difficult, leading to increased inventory costs, longer lead times, and lower customer satisfaction.
Inefficient Processes: The semiconductor industry involves many processes, from design to manufacturing to testing and packaging. Without an ERP system, managing these processes can be challenging, leading to inefficient workflows, redundant work, and a lack of visibility into the entire process.
Limited Visibility: Without an ERP system, semiconductor companies may have limited visibility into their operations, including production capacity, inventory levels, and order status. This can make it difficult to make informed decisions and respond quickly to changes in demand or supply.
Without integrating with ERP: As semiconductor companies grow, managing their operations becomes more complex. Without an ERP system, managing growth can be difficult, leading to a lack of scalability and the need for manual processes that can limit productivity and efficiency.
Following are the few drawbacks Without integrating MES with ERP
High Demand equals High Pressure:
Looking beyond electronics and telecom, nearly every industry segment in their pursuit of Industry 5.0 needs semiconductors. Chip demand is booming and so is the need to focus on design wins, deliver more through existing capabilities while adding new ones, add new processes and products. MES needs to evolve to reduce these challenges.
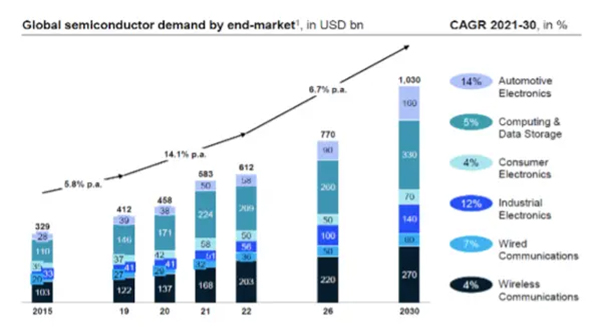
MES for Semiconductor Industries
An MES helps achieve that goal by tracking and gathering accurate, real-time data about the complete product lifecycle, beginning with order release until the product delivery stage for finished goods.
The MES collects data about product genealogy, performance, traceability, material management, and work in progress (WIP), and other plant activities as they occur. This data, in turn, allows decision-makers to understand the current situation of the factory floor and better optimize the production process.
Digitally controlled and monitored workplaces nurture an increased bottom line. In a manufacturing company, tracking and capturing the entire business data is paramount.
A Manufacturing Execution System offers tools for the execution phase in the production process. Specifically, the period between when a production order has been released to the production floor and until the work is completed.
While the key task of MES is the ability to have an intuitive and easy way of starting and reporting back on production jobs, it also supports the daily planning happening on the shop floor, this includes prioritization of one job over another, assigning jobs to resources where resources are either individuals or groups of workers or individual or groups of machines or even in some cases vendors operating on part of the production process
IBM SiView MES for Semiconductor Industries
Semiconductor companies face a growing set of challenges to manage opportunities, from identification through production in an increasingly complex global ecosystem.
Volume growth, coupled with downward pressure on margins and average selling prices (ASPs) are straining manufacturers’ ability to develop and manage their product portfolio.
SiView standard is also difficult to plan and schedule across complex manufacturing lines located worldwide.
SiView Standard can transform your manufacturing execution systems (MESs) and processes by helping you get your semiconductor line up, running and stabilized early, and improve supply chain management through a unified system. SiView Standard can provide a competitive edge with a fully automated, single wafer control, and build a line to handle multiple lots in a carrier.
SiView Standard can improve your strategic sourcing, collaboration, and enterprise resource planning to support manufacturing processes.
SiView Standard integrates with your current enterprise systems to facilitate tighter supply chain and manufacturing linkages, so you can leverage economies of scale and respond quicker to market changes.
Source : IndustryView for Semi-Conductor Standard – Overview | IBM
Solutions ERP offers to overcome limitation in Semiconductor Industry
The primary reason why businesses combine both systems is to move towards smarter manufacturer, and it will help to smoothen manufacturing activities.
An ERP (Enterprise Resource Planning) system can provide many solutions for the semiconductor industry, including:
Centralized Data Management: An ERP system can provide a centralized platform for managing data, including product specifications, manufacturing instructions, test results, and process parameters. This can help ensure data accuracy, reduce data silos, and improve data visibility across the organization.
Streamlined SCM:
An ERP system can help semiconductor companies improve their supply chain management by providing real-time visibility into inventory levels, order status, and production capacity. This can help optimize inventory levels, reduce lead times, and improve customer satisfaction.
Improved Process Efficiencies:
An ERP system can help semiconductor companies streamline their processes by automating manual tasks, improving workflow visibility, and reducing redundancies. This helps errors, improve quality, and increase productivity.
Real-time Visibility: An ERP system can provide real-time visibility into key performance indicators (KPIs), such as production volume, yield test, and cycle times. This can help semiconductor companies make informed decisions, respond quickly to changes in demand or supply, and identify areas for process improvement.
Scalability: An ERP system can provide a scalable platform that can grow with the needs of the semiconductor company. This can help support growth, reduce the need for manual processes, and increase productivity and efficiency.
Example of one of the flows from MES – ERP and vice versa
Toward Smarter Semiconductor Manufacturing
The future of ERP (Enterprise Resource Planning) for the semiconductor industry looks promising, as modern technology advancements and industry trends continue to shape the way semiconductor companies operate. Here are some potential future developments for ERP in the semiconductor industry:
Integration with IoT and AI:
The integration of ERP systems with IoT (Internet of Things) and AI (Artificial Intelligence) technologies can enable real-time data collection, predictive maintenance, and more efficient production processes. This integration can help semiconductor companies optimize their operations, reduce costs, and increase productivity.
Cloud-based ERP Systems:
Cloud-based ERP systems can offer several advantages over on-premises systems, including scalability, cost-effectiveness, and flexibility. As the semiconductor industry continues to grow and change, cloud-based ERP systems can provide the necessary agility and scalability to meet new demands.
Increased Use of Analytics:
The use of analytics in ERP systems can help semiconductor companies make better business decisions by providing insights into trends, patterns, and opportunities. With the increasing amount of data generated by the semiconductor industry, analytics can play a key role in optimizing operations and improving decision-making.
More Emphasis on Security:
With the growing threat of cyber-attacks, security will continue to be a top priority for semiconductor companies. ERP systems will need to integrate robust security features to protect sensitive data and prevent cyber threats.
Greater Focus on Sustainability:
As the demand for sustainable practices increases, ERP systems will need to support sustainability initiatives, such as tracking carbon emissions and reducing waste. This will require more comprehensive tracking and reporting capabilities within the ERP system. Sustainability will be maintained or increase using industry 4.0 and 5.0 which offers by ERP.
Real-time OEE & Digital Dashboard :
Collecting real-time data of availability, performance and Quality, the system provides an accurate OEE numbers in the dashboard with drill down capabilities. They can see the improvements immediate after deploying the solution.
ERP-MES integration in Industry 5.0 :
Industry 4.0 – or the Fourth Industrial Revolution – brought “smart” technologies such as artificial intelligence (AI), cloud connectivity, and real-time data analytics to the world of industry and manufacturing. At the core of the industry 4.0 revolution is a drive toward efficiency, productivity, and hyperphysical systems.
While in production you need real-time flexibility and agility, ERP cannot help and guide operators, analyse bottlenecks, control, and improve product quality, or do last-minute product adjustments – all things very much needed in today’s Industry 5.0 environment.
Conclusion :
With new powerful cloud capabilities to leverage, ERP modernization is top-of-mind. But, connections across the broader ecosystem cannot be overlooked. Legacy integration tooling often fails to optimally support ERP modernization, slowing productivity and potentially disrupting business. Focusing on the overall integration architecture is a unique opportunity to maximize ERP implementation benefits and transform with confidence. ERP Integration solutions optimize ERP system integration operations, while reducing the cost and risk of ERP transformation projects.
There are several challenges using MES in semiconductor industries to capture day to day activities and from digitisation point of view. Challenges faced by semiconductor industries can be overcome MES-ERP integration. This will help digital transformation within the Semiconductor industry to continue and accelerate. Most of the chip manufacturing companies are already did digital transformation.
Bringing MES solution integrated with ERP delivered substantial benefits and create better understanding and continuous improvement to meet complex semicon process requirements.
Full automation in semiconductor assembly and test is no longer a myth. While the legacy of the assembly and test segment has relied heavily on manual methods, primarily driven by lower costs in eastern parts of the world, the current reality demolishes this premise.
The complexities of the modern supply chain, as well as the emerging complexities in technology, products, equipment, and processes, necessitate the urgent need to adopt automation methods. The exponential growth of automotive, smart computing, communication, and Industrial Internet of Things (IIoT) content in the product-mix serves as a catalyst to this adoption.
The automotive segment represents a significant leap in quality requirements and factory capabilities. Lastly, current processing and supply chain requirements have made it nearly impossible for a human to comprehend simple processing tasks such as lot selection and lot transport.
MES is focused on the shop floor, keeping production in line and controlling the building of parts. ERP systems are primarily responsible for managing inventory, sales orders and shipments. Having these systems communicate with each other is essential. If you have both, it’s kind of crazy not to link them together. The benefits are about visibility.
While the functions of MES and ERP have always intermingled and overlapped, modern best practices suggest a conscious fusing of the two into a seamless data resource. While the two systems continue to maintain their own identities and functions, improving the way they communicate with each other provides benefits for the entire organization.
Getting the most out of both of your systems means that you will have to unite them. Once you have meshed them together, your organization will realize entirely new paybacks that each system could not provide on its own.
To transform into Industry 4.0 and Industry 5.0, the implementation of an MES or ERP would be sufficient. However, more than just implementing these systems is needed to achieve total efficiency in production processes. This is where IoT comes in.
About the Author :
Mr. Shivam Mhapankar PMP®ITIL®
NextGeN ERP Account & Business Development Executive -Hi-Tech Industry
IBM Consulting
Shivam is the Sr. SAP S/4 HANA Program Manager & Business Development Executive for the Hi-Tech Industry, for IBM Consulting-CIC India. He has a 20+ years track record driving innovation and changes in the Electronics Industry in supply chain operations, information technology, and enterprise business transformation to enable profitable revenue growth. He has broad-based strategic, business, consulting, and project management skills gained over years of experience in the industry.
Mr. Shivam Mhapankar PMP®ITIL® is Bestowed with the following Licenses & Certifications :
https://www.linkedin.com/in/sh
Mr. Shivam Mhapankar can be contacted at
Mobile : + 91-99308 61764
E-mail: [email protected], [email protected]
LinkedIn : shivam-mhapankar-9a79731b7
Mr. Rushikesh Pawale
SAP PP Consultant, IBM – CIC India.
Mr. Rushikesh Pawale has a wide knowledge about manufacturing industries. He has accorded with Business and consulting skills.
Mr. Rushikesh Pawale can be contacted at:
Email : [email protected]
LinkedIn : https://www.linkedin.com/in/rushikesh-pawale-a768081b7/
Mobile : +91 96898 73635
Also read Mr. Shivam Mhapankar‘s earlier article :