REMOTE CONNECTIVITY GATEWAY FOR PLC UNDER INDUSTRY 4.0 INITIATIVES
INDUSTRIAL REVOLUTION AND ASPECTS OF INDUSTRY 4.0:
Industry 4.0 represents the fourth industrial revolution in manufacturing and industry. Industry 4.0 is the current industrial transformation with automation, data exchanges, cloud, robots,Big Data, AI, IoT, and autonomous industrial techniques to realize smart industry and manufacturing goals in the intersection of people, new technologies, and innovation.
Industrial automation is no longer limited by the walls of a production facility. According to a report an Indian Industrial Automation Market size was valued at USD 5 Billion in 2018. It is further expected to grow at a CAGR of 12% by 2023. There is more and more automation are being handled and controlled via remote communication. The mainly automated industries are like Oil and Gas Industries, Pharmaceutical Industries, Paper and Pulp Industries, Automobile Industries, Manufacturing and process Industries. No matter it’s from the office or from the comfort of your own home or a cafeteria. Today’s PLCs give you the ability to access your control system to handle such tasks as monitoring via a website to determine the condition of a machine or check other statistics. Let’s look at various at various aspects of Industrial Revolution to understand the industry 4.0 that is the need of the hour.
Scenario
- Demand for highly customized products
- Short product life cycle
- Highly competitive markets
- Environmental restrictions
Customization
- Highly flexible production lines
- Productive and cost effective
- Make to order
Technologies
- IoT, Cyber Security, AI, Big Data, Cloud Computing
- Automation and Robotics
Brownfield to Digital IoT Enabled Factory:
As per Capgemini research that smart factories could contribute an annual added value of $500 billion to the world economy in the next five years and overall productivity is expected to increase by at least 27% each year, and smart factories could account for up to 60% of all manufacturing plants by 2022.
Most legacy assets, machines, and facilities across industries were not designed to connect beyond plant networks, creating huge data silos within the factory. This leaves companies with two choices: Building entirely new, greenfield plants with native IoT technologies OR Updating brownfield facilities for IoT connectivity. The first approach is very expensive. Typically, in auto & other manufacturing, a greenfield smart factory setup is estimated to cost from $1 billion to $1.3 billion – around 200 times as much as a brownfield. Besides, as industrial systems are very capital intensive and often have a long lifespan of several decades, completely replacing them is not a choice for most manufacturers.
Let’s understand below 3 approaches:
- Retrofit Assets and Equipment with IoT Sensors
- Enable Existing PLCs with IoT Connectivity
- Substitute Remote I/O Units with IoT-Connected Ones
Connect Legacy Machines to the IoT Connected Age – Advantages of IoT:
All these functions are now within reach of all industrial facilities, regardless of size or budget. Legacy factory equipment has been largely left out of the IoT revolution, but has continued to be a serious concern for our clients. Some legacy factory machines simply cannot be replaced cost effectively, and must be modernized for the IoT.
- Most Efficient and Reliable way to Monitor machines health
- Track faults weeks in advance, monitor machines from miles away
- Generate work orders, and shut down machines before catastrophic damage occurs.
Connect Legacy Machines to the IoT – Challenges & Strategy:
- Traditional/Legacy machines are controlled by PLC, SCADA, VFD or a local control system
- Challenge: Difficult to extract data to be sent to cloud
- Strategy: Try to bring these legacy machines into the IoT world without altering or modifying the existing installation.
- Let’s understand Challenges in the categories of Legacy Machines: Primitive and Intelligent Machines
- Primitive machines: No provisions for modernization, no integrated sensors, no integrated communications protocols, and no controls systems.
- Strategy: Required frequent upgrades with external sensors to visualize machine operations
- Intelligent machines: Have provision for an integrated control system, such as a custom PLC, or other control computer to help the machine execute a specific task.
- Strategy: Mostly provide access to RS-485 or RS-232 Ports, or may have 4-20mA outputs or inputs to help monitor and control machine operation. These machines can be upgraded with specialized hardware for converting older data types into modern IoT data types.
- Primitive machines: No provisions for modernization, no integrated sensors, no integrated communications protocols, and no controls systems.
The latest generation of PLCs have an integrated Ethernet port on the controller for two main operations. The first is controlling remote I/O on Ethernet based protocols like EtherNet/IP, Profinet, or Modbus/TCP to name a few. The second is to program and/or debug the internal program of the controller. With these features, and utilizing the Ethernet’s other services such as a web and ftp server, remote administration of a control process becomes possible.
Current Situation and it’s Problem
For the situations like current pandemic situation or work from home. There is need of remote commissioning of PLC and SCADA. Due to pandemic or any realistic problem if the PLC programmer, SCADA Developer or Process Supervisor is not able to come to office. Then how will be the PLC programmed and supervised. Is there any solution for this?
HEXAEDGE NETWORK’S REMOTE CONNECTIVITY SOLUTION
Firstly, you should have a PLC with an Ethernet port. Then first step in connecting remotely is the PLC with an Ethernet port to handle communication from both the local network as well as, handle messages from a wider network such as the internet. This is accomplished by adding a gateway address to the Ethernet communication settings on the controller. Thereby, allowing the controller to send and receive IP messages that are not established inside the local network.
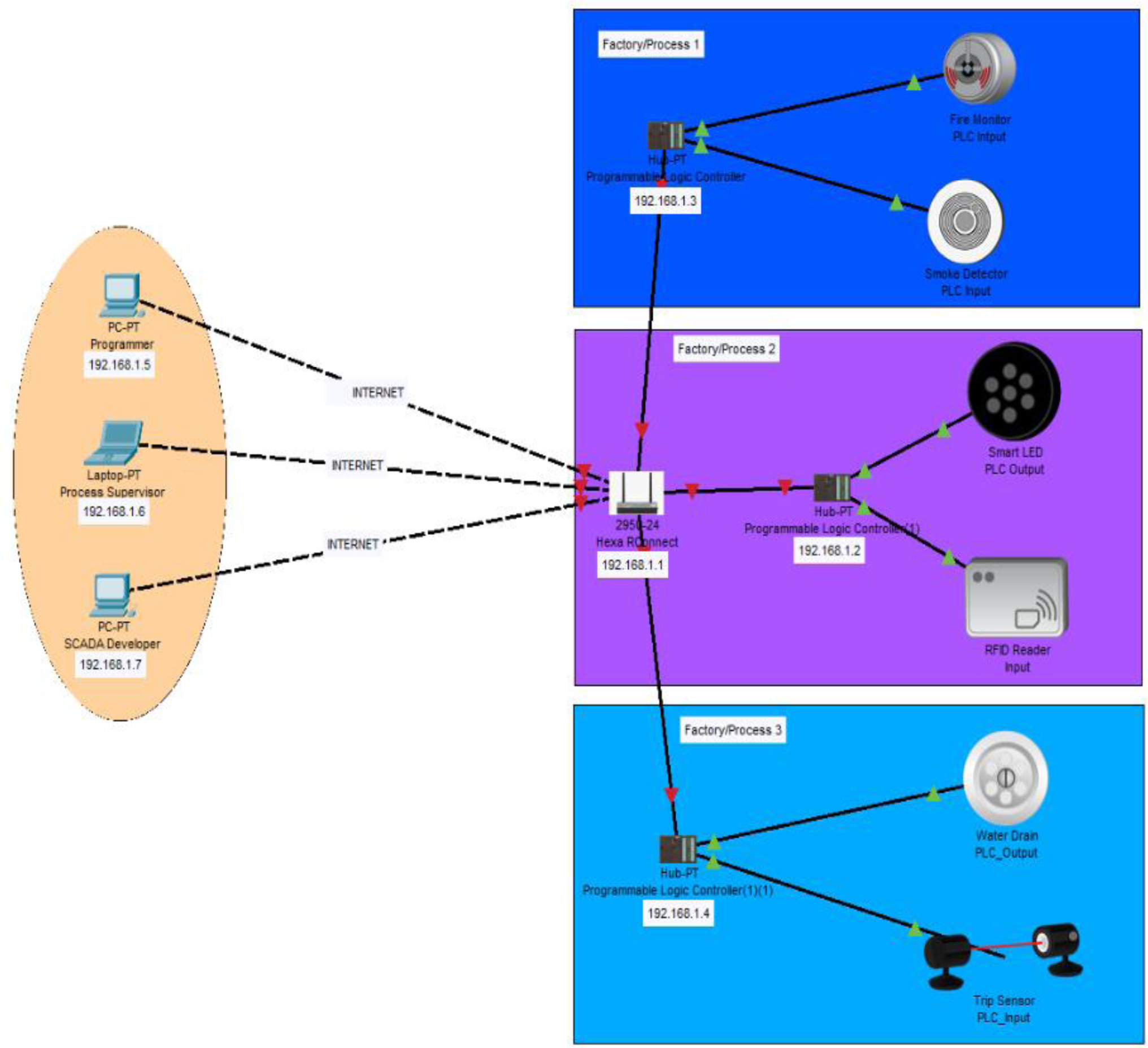
PROTECTION
By attaching a programmable logic controller to a network with Internet access, the device will be exposed to all of the same possible security threats as a computer. Hexa RConnect provides private network over internet for the security of data. For the commissioning of PLC remotely there is no static IP required. End to end encryption is provided for avoiding vulnerable activities.
CONCLUSION
Applying these simple techniques to modern day control networks using Hexa RConnect to PLC, new options are available for the control and commissioning of process for industries. Data collection over great distances is one of the best uses for this technology. You can monitor the process and troubleshoot the PLC from the ease of your place. Retired experienced employees can also give the training to new employees of Industry from their home. One can easily program, control, monitor and troubleshoot the PLC from their home.
Mr. NDVS Ramakrishna Rao Dr. Prashant K Lahane
Co-Founder & Director Co-Founder & Director
They can be contacted at +91 93215 85837
Email – [email protected]
Web – www.hexaedgenet.com