Industrial Internet of Things (IIoT), artificial intelligence (AI), big data analytics, edge & cloud computing, and such other digital technologies are beginning to transform the global manufacturing industry. The exponential growth of the processing and computing capabilities of microprocessors, their availability at affordable prices, and their miniaturization & robustness have contributed to the growth of digital technologies and their accelerated convergence with the manufacturing. IIoT refers to interconnected sensors and other devices networked together for industrial applications. AI refers to machines or computers that perform cognitive functions that are associated with the human mind, such as learning and problem solving. Big data analytics is the processing of large amounts of data to uncover hidden patterns, correlations and other insights. While edge computing is a distributed computing paradigm that brings computation and data storage closer to the location where it is needed, to improve response times and ease of communication, cloud computing is the on-demand availability of computer system resources, especially data storage and computing power, such as remote data centers available to many users over the Internet.
The use of digital technologies empowers manufacturing companies to collect large amount of data, convert them into information, share the same among all the stakeholders in real-time, process them for obtaining actionable insights, and autonomously act on them. As a consequence of the application of digital technologies, right people operating the manufacturing plants get access to the right information at the right time and this contributes to operating the plant more productively, competitively and achieving manufacturing excellence.
This transformation of the manufacturing industry is described variously as digitalization, fourth era of industrialization, and Industry 4.0 and these words are often used interchangeably. These words essentially refer to the use of digital technologies in the manufacturing companies. While digitalization is the technical description that explains the process of empowering manufacturing companies in the application of digital technologies, fourth era of industrialization is more appropriate description when viewing the development from a historical perspective. At the industry and policy making level, Industry 4.0 is commonly used. Digitalization is the process of leveraging digital technologies to connect equipment / machines, data & people, process the digitized information to gain actionable insights that can be acted upon to achieve operational efficiencies and productivity improvements in manufacturing enterprise’s processes and operations. The fourth industrial revolution, a description coined by Klaus Schwab, executive chairman of the World Economic Forum, is the ongoing automation of traditional manufacturing and industrial practices, using modern digital technologies. The first era of industrialization refers to the end of 18th century that witnessed the introduction of water and steam equipment to help humans in performing some of their tasks. The early part of the 20th century that witnessed the use of electricity and steel is considered as the second phase of industrialization. In the late 20th century, production processes began to use computer and communication technologies, ushering the third era of industrialization.
Industry 4.0 is an initiative started by the German Government in 2006 with the goal of increasing its manufacturing industry’s productivity by leveraging the digital technology. Similar initiatives have been taken by other countries, the example being America’s Advanced Manufacturing Partnership 2.0, South Korean Manufacturing Industry Innovation strategy 3.0, and China’s Made in China 2025. Make in India, an initiative launched in 2014, while encourages companies to manufacture in India, focuses on job creation, enhance manufacturing sector’s growth to 12-14 per annum, and increase its contribution to the country’s GDP to 25percent by 2022. Make-in-India is the closest overarching initiative by India’s policy makers but its focus is not on increasing the sector’s productivity or competitiveness through the use of digital technology.
The primary challenge facing the India’s manufacturing industry is to enhance its productivity and competitiveness and this is correctly emphasized by McKinsey in its report ‘A new growth formula for manufacturing in India.’ The report highlights that India’s manufacturing industry needs to become more productive and globally competitive through the technology route. It points out India’s labor productivity and capital productivity are low compared to its global peers and prescribes that ‘India’s manufacturing value chains must lift their productivity.’ It says ‘Compared to India, manufacturing productivity in Indonesia is twice as high; in China and South Korea, productivity is four times higher;’ ‘South Korea’s electronics manufacturing sector is 18 times more productive than India’s, and its chemicals manufacturing sector is an astonishing 30 times more productive.’ It goes on to say that ‘Improvements to key manufacturing processes could increase the productivity of Indian companies’ by adopting Industry 4.0 / digitalization approach. A manufacturing firm, through comprehensive and effective digitalization, can generate actionable information by aggregating data relating to suppliers, material availability, customers, enterprise resources, available production capacity, equipment availability, etc. Thus a manufacturing firm through digitalization can attain tighter integration of numerous operations and efficient collaboration across departments, value chain partners, customers, & others and achieve manufacturing excellence. The world of manufacturing is going through a metamorphosis and the captains of the country’s manufacturing should take the necessary steps to be in synch with this trend; and it is essential for them to move forward with digitalization in order to protect their own interests and stay relevant in future.
About the Author
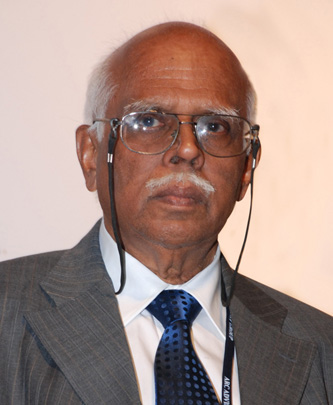
Mr. Rajabahadur V. Arcot
Independent Industry Analyst, Columnist and Automation Consultant.
Life Member of ISA.
Member of ISA Smart manufacturing & IIoT Division.
ISA accredited mentor and trainer.
He authors industry & technology articles, market research reports, case studies, white papers, automation & manufacturing IT insights.
He can be reached @ 98452 09442 / [email protected]