Technical Training Trends – Industrial Automation & Robotics for Manufacturing Excellence
More than 80% of engineers in India are “unemployable”. This is the report submitted by Aspiring Minds, an Indian employability assessment firm, after a study of about 150,000 engineering students in around 650 engineering colleges across India. Out of the millions of engineers who graduate each year in India, only 3% were found to possess 21st Century skills including AI, Machine Learning, Data engineering and Robotics and the aggregate employability in these domains was found to be around 1.5%.
Our education system has not kept up with the pace of global technological advancements. At the same time, the demand for specialised skills from industries has only increased. Today we are witnessing millions of graduates left to fend for themselves in an ever -changing technological landscape.
Aspiring Minds further reported that only 40% of engineering graduates end up doing an internship and 36% do any Projects beyond coursework, thereby limiting their exposure to industries. Lack of practical, application – oriented curriculum and exposure to experiential learning has reduced the employability of engineering graduates.
Lack of skilled talent would mean industries must train people from scratch, significantly increasing their operational costs and complicate the hiring process, which acts as a major inhibitor for recruitment.
Today we are facing a two-pronged issue. On one hand, there are millions of fresh graduates who need training in the latest technologies. On the other side, millions of professionals are increasingly becoming redundant and in need immediate upskilling.
For example, a recent survey showed that around 40 percent of IT professionals in India need to upskill themselves over the next few years while 48 percent of companies report difficulties filling job vacancies due to talent shortages.
More than unemployment, experts agree that India is facing a major shortage of skilled talent. The common consensus is that there are enough jobs for skilled manpower in India. India is about to become the world’s youngest nation by 2020 with about 64 percent of it’s population in the working age, and the need of the hour is to upskill the workforce with technologies of future for Manufacturing Excellence.
Out of the workforce of 421 million (aged 15-59 years), only 2.5% have acquired technical education. To achieve Government of India’s Make in India and Skill India initiatives, we need to upskill around 291 million people by 2022, out of which 136 million need to receive formal Vocational Training.
A study on 2018 skills gap in manufacturing, published by Deloitte says Robotics & Automation is the key skill in future Manufacturing workplaces.
Some of the future Manufacturing work personas, as published by Deloitte include – Digital Twin Engineers, Predictive Supply Network Analyst, Robot Co-ordinator, Digital Offering Manager and Drone Data Co-ordinator. Digital transformation and Industry 4.0 continues to redefine manufacturing jobs and the work environment of the future is expected to blend advanced technologies with human “soft” skills to yield maximum productivity.
In India, we expect a shortage of 3.5 million skilled manpower in Automation and Robotics by 2022. Industrial IoT / Data Analytics will have a shortage of 200,000 professionals in the next three years. We have an opportunity to upskill our young workforce and become a world leader in the technology-driven future.
The upskilling must start at grassroots level. STEM courses during secondary and tertiary level of education would greatly help in building interest in manufacturing and technology -oriented careers. Intern programs and shadowing experiences in Industries will enable them to get a real-time understanding of the Manufacturing sector.
Traditionally, Indians are known to perform better in a personalized, one – on – one mode of learning. This is where Technical Training Campus’ in Industrial Automation and Robotics with Real-time Industrial infrastructure come into play.
Synergistic efforts from the Government, Industry bodies, Corporate Organizations, Educational Institutions and Advanced Technical Training Campuses towards skill and infrastructure building is the need of the hour to enable the emergence of India as a global power in the era of digitized manufacturing.
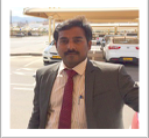
Engr. Sathesh Selladurai is the Co-Founder & Director, Axis Global Automation Group and Axis Global Institute of Industrial Training is an Electrical and Electronics professional and is responsible for implementing Technical projects across India, the United Arab Emirates, Sultanate of Oman, Indonesia, Sri Lanka, Singapore and Malaysia. Armed with strong technical expertise and over 12 + years of industry experience, he spearheads the group’s manufacturing, testing, commissioning and other technical activities. Axis Global Group also represents Yaskawa Motoman, Japan.